Carbon Fiber Resin Jetting (1)
- Kyung Hun Jung (Virginia Tech Senior Design Team)
- Feb 13, 2018
- 2 min read
Our 3-D printer jets resin through the printer head, binding the carbon fiber in shapes. The main method is Resin Jetting.
Problem Statement
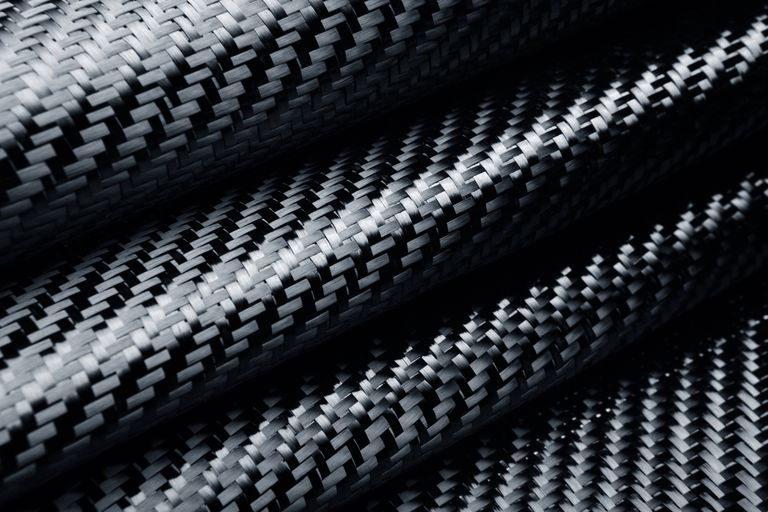
Main Problem:
- The existing carbon fiber reinforced parts are brittle
- Printed parts are created with a low concentration of carbon in the existing carbon fiber 3D printers

Goals:
- Improve the elongation and energy absorption of the 3D printed parts
- Print samples with a higher percentage of carbon
Requirements and Specifications
Our team provided requirements and specifications for the printer:
"The most important need from our customer is the 3D printer's ability to print carbon fiber, to print parts without cracks, and to print parts with high energy absorption. Based on the customer needs, the most important engineering characteristics for our design are density, sample yield strength, and sample strain limit."

Concepts Generation and Selection
Our team generated about 5 different concepts using various printing methods such as multi extruder FDM printing, 5-axis FDM printing, multi material SLA printing, and Powder based binder jetting printing. We narrowed down to two final concepts via down selection.

Concept 1 - Multi Material SLA
- Uses a fixed UV light source and a moving print window with multiple materials as resin.
- Use two Resins:
- Carbon Fiber Powder + Resin
- Flexible Resin
- Advantages
- Higher resolution printing with smoother surface
- Higher energy absorption
- Disadvantages
- Carbon Fiber absorbs UV light which prevents curing

Concept 2 - Carbon Fiber Resin Jetting
- Uses heat-curing resin to bind carbon fiber powder together
- Advantages
- No requirement of support
- Higher percentage of carbon fiber
- Wider range of materials
- Disadvantages
- Limitation for closed hollow structure
- Only works with powdered material
CAD
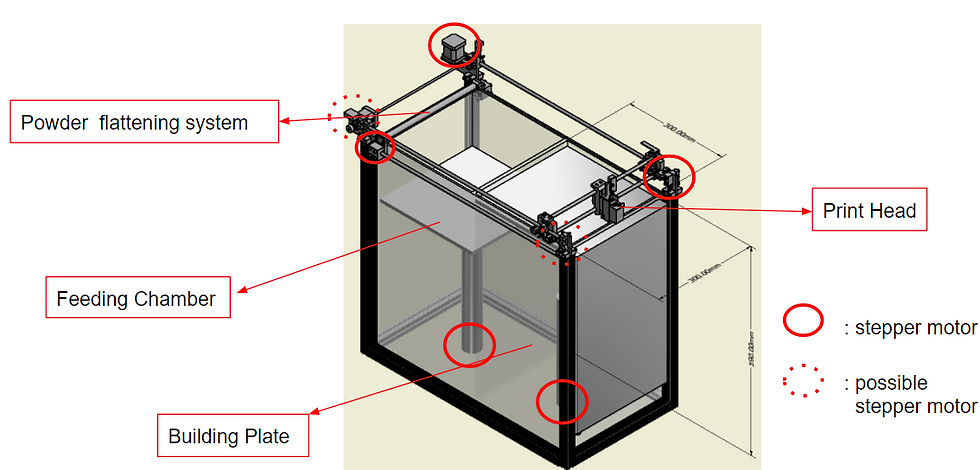
This is the first version of the 3D CAD model printer that we desgined.
The key technology for this printer is the use of thermal-curing resin and the distribution of it into carbon fiber powder. The Printer prints layer by layer, and after every layer, the build piston moves downward while the feed piston moves upward for the next print layer.
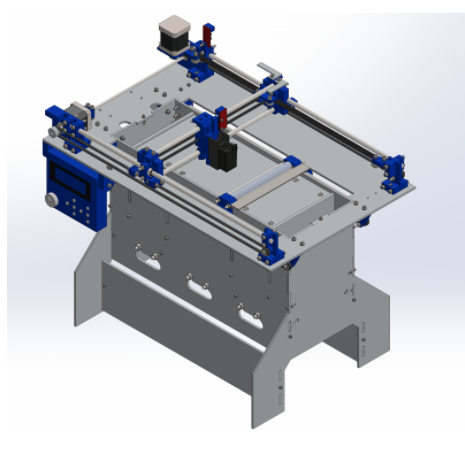
Our team downloaded a CAD file from an open source of powder-based 3D printer from: https://ytec3d.com/plan-b/
This printer is well designed with great details, so our team decided to work on this design instead of using our design. This saves lots of time and allows us to focus on studying powders and resin, and gives us a strong basic knowledge on powder based 3D printing.
However we might add some more features such as heat curing sources as we change our resin.

Comments